Reorder Point Formula; the Right Calculation For Your Business
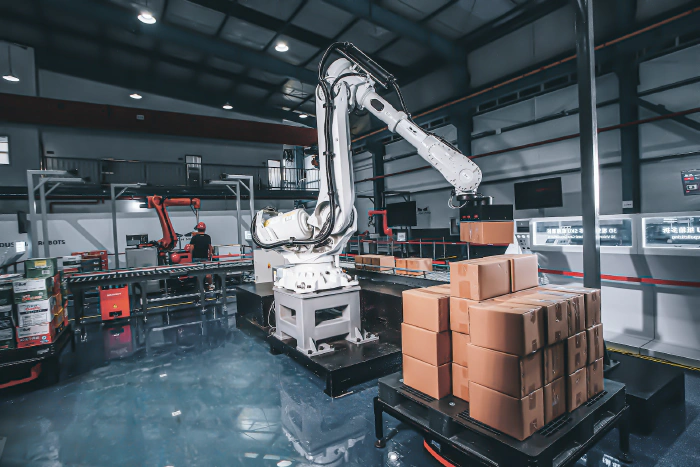
When is the right time to reorder stock for your inventory? It’s a question retailers have tussled with for a long time and it’s the reason for the reorder point formula. With the right reorder point in place, you reduce the prospect of running out of stock, while also making sure you’re not carrying too much.
In this article, you’ll learn what a reorder point formula is, including the associated key metrics, how to calculate it, why it’s important and some strategies for getting your reorder point right.
Table of Contents
- What is a Reorder Point?
- Reorder Point Formula Key Metrics
- How to Calculate the Reorder Point Formula
- Reorder Point Formula Without Safety Stock
- Why is Your Reorder Point Important?
- 7 Strategies to Get Your Reorder Point Right
- Get the Right Reorder Point With Singuli
What is a Reorder Point?
A reorder point is the moment a business needs to place an order to make sure their inventory doesn’t drop to a dangerous level, or even to zero. Many factors are taken into consideration when calculating the ideal reorder point for each product in your business, including lead time, demand and safety stock levels.
Reorder Point Formula Key Metrics
There are a few vital metrics that you need to consider when calculating your reorder point formula:
Demand
Forecasting demand is one of the trickiest aspects of any business and it’s one of the reasons inventory optimization software exists. For the most accurate inventory forecasting, you need to consider size curves, seasonality, trends, unexpected spikes in demand and much more. With accurate demand, you can calculate a better reorder point.
Lead Time
If you know how long it takes from the moment you place an order to the moment your goods are received, you know your lead time. Most businesses calculate this using days.
$$\text{Lead time (days)} = \text{delivery date} - \text{order date}$$
Lead time example:
- Delivery date = April 30
- Order date = April 21
Lead time (days) = 30 - 21 = 9
💡Pro Tip: Maintain optimum stock levels and adjust to sudden changes by using Singuli to manage multiple vendors and products with different lead times.
Lead Time Demand
When you know your demand and your lead time, you can work out your lead time demand. This is simply the demand for your product between your order date and your delivery date.
$$\text{Lead time demand} = \text{lead time} \times \text{demand}$$
Lead time demand example:
- Lead time = 9 days
- Demand (per day) = 6 units
Lead time demand = 9 × 6 = 54 units
Safety Stock
The average safety stock formula is the most common and the one we’ll use in this example, although there are many alternatives. Safety stock mitigates the risk of sudden surges in demand or increases in supplier lead times.
$$\text{\footnotesize Average safety stock} = \left(\text{\scriptsize max daily units sold} \atop \overset{\times}{\text{\scriptsize max lead time in days}}\right) - \left(\text{\scriptsize average daily units sold} \atop \overset{\times}{\text{\scriptsize average lead time in days}}\right)$$
Average safety stock example:
- Max units = 8
- Max lead time = 6
- Average units = 6
- Average lead time = 4
Average safety stock = (8 × 6) - (6 × 4) = 24 units
💡Pro Tip: Plan for multiple versions of the future with Singuli’s Scenarios. Ask “what if” and get answers immediately
How to Calculate the Reorder Point Formula
Although there’s a lot to think about if you want to get the perfect reorder point for every product, every time, the basic reorder point formula is quite simple:
$$\text{Reorder point} = \text{lead time demand} + \text{safety stock}$$
Reorder point example:
- Lead time demand = 54
- Safety stock = 24
Reorder point = 54 + 24 = 78 units
If you use the right software to work out demand, you’re more likely to implement a reorder point that stops you having to use safety stock or at the very least stops you from running out of stock altogether, without ordering so much that your carrying costs become unmanageable.
Further reading: 27 Important Inventory Formulas to Improve Your Planning
Reorder Point Formula Without Safety Stock
Safety stock is important for most businesses and it’s rare to need to calculate a reorder point without safety stock, but there are some occasions where it makes sense. For example, if you’re resupplying from your own warehouse and don’t have to account for unexpected supply chain delays or if you buy products using JIT (just in time). Restocking with JIT means you bring in inventory for the exact moment you need to sell it, so you don’t use up warehouse space. You need a seamless supply chain with many redundancies for this to work well.
Why is Your Reorder Point Important?
Not getting your reorder point right can cause problems with suppliers, customers and internally. Let’s see how the right reorder point can benefit your business:
Avoid Stockouts
Stockouts happen when you don’t have enough inventory to meet demand. They can cause you to lose sales and even to lose customers permanently. If you don’t have the correct reorder point in place, they will happen more often.
💡Pro Tip: Create accurate forecasts to prevent stockouts using Singuli’s Advanced Demand Forecasting.
Minimize Overstocks
Having too much stock might not seem like as big of a problem as having too little, but there are a lot of carrying costs associated with overstocks and you could be using up space better served by faster-selling products. If your reorder point is too early, overstocks are more likely to happen.
📌Get Started: Avoid stockouts and overstocks by understanding the perfect inventory turnover rate (ITR) with Singuli’s Advanced Demand Forecasting.
Improve Forecasting
A more accurate forecast and a more accurate reorder point go hand in hand. Accurate demand forecasting allows you to choose a reorder point to anticipate future demand. When your reorder point is more accurate, you can use the demand data you gather from each order to better forecast.
📌Get Started: With Singuli’s Advanced Forecasts, it’s easy to analyze historical data, market trends and customer inputs, which saves you or your inventory planner time and increases forecast accuracy.
Reduce Inventory Costs
Inventory costs are shipping costs, storage costs and all the other costs that come with holding onto too much inventory. Getting your reorder point right means you’re not holding onto stock that you don’t need and that you have the space to improve your inventory planning, which means you’ll only add inventory costs that are necessary for your business to run.
📌Get Started: Optimize your inventory levels and reduce overstocks. Use Singuli to replenish the right amount of stock at the right time so your inventory costs stay low.
7 Strategies to Get Your Reorder Point Right
It can take time, but with good software and the right strategies, you can get the best reorder point for your business. Here are seven strategies you can use.
1. Implement Your Reorder Point
Working out the right reorder point is vital, but if you don’t implement it, it’s a thankless task. Make sure you actually act on the reorder point notifications or set up automatic reordering if you’re confident in your supply chain and any other variables.
2. Avoid Using an Absolute Reorder Point
Demand is almost never a straight line. It increases and decreases without warning. You can use inventory optimization software to improve accuracy, but simply reordering the exact same amount at exactly the same time will only cause problems.
3. Make Use of Inventory Forecasting
Inventory forecasting predicts stock levels by using historical data, trends and future events. With the right software, you get a much more accurate idea of the stock quantities you need to meet demand without overstocking, and you discover the perfect moment to replenish and reorder stock.
💡Pro Tip: Optimize your inventory with Singuli software, which acts as a valued member of your team.
4. Understand Your Data
There’s a lot of data involved in accurate inventory planning. Size curves, ABC analysis and future scenarios are just a few of the data points to think about. Software helps to organize your data and to use the relevant information at the right time, so you can reorder just when you need to.
5. Efficiently Manage Your Supply Chain
Strong supplier relationships and a range of suppliers create flexibility and stability when you’re reordering. You know who’s reliable, what your lead times are and what your redundancies are. If something goes wrong with a supplier and you have a good relationship, you’re more likely to be looked after before your competitors.
📌Get Started: See every stage of your supply chain with Singuli’s Visual Timelines so you never miss a beat.
6. Use Software to Automate Your Reorder Point
The best inventory planning software can automate your reorder point. This saves you time and allows you to concentrate on growing your business. Instead of working out the right moment for every product and constantly adjusting for changes, you can let your software do the work and simply check it periodically.
7. Take Care of Your Inventory Optimization
Inventory optimization balances demand needs with capital and resources. Demand forecasting, inventory classification, efficient supply chain management and effective inventory control systems all play a role in getting your inventory optimization right. When those factors are running smoothly, you have more accurate data to base your reorder point on.
Get the Right Reorder Point With Singuli
Your reorder point is crucial to meeting demand and minimizing costs, so you need to get it right. Save time on calculating reorder point formulas—let Singuli do it all for you instead.
Forecast demand, issue and track POs, re-order on autopilot, and step up your reporting game across multiple channels and locations. Get in touch to see how Singuli can help you optimize your inventory.
Reorder Point Formula FAQ
What is the Reorder Point in the EOQ Model?
The EOQ (economic order quantity) reorder point is a formula that determines the best possible time to reorder products, based on cost.
What is an Example of a Reorder Point With Safety Stock?
Most reorder point formulas take account of safety stock. Safety stock is in place to mitigate the risk of sudden supplier changes or spikes in demand. When you add safety stock to the anticipated demand across a delivery lead time (lead time demand), you calculate the reorder point.
Reorder point with safety stock:
- Lead time demand = 48
- Safety stock = 21
Reorder point = 48 + 21 = 27 units
What is the Difference Between Reorder Point and Safety Stock?
Your reorder point is the ideal moment to place an order with a supplier to replenish stock. Your safety stock is a backup to make sure you don’t completely run out of inventory in case of delays or unforeseen spikes in demand.
Forecast demand, issue and track POs, reorder on autopilot, and step up your reporting game across multiple channels and locations. Get in touch to see how Singuli can help you optimize your inventory.