Inventory Carrying Costs: How to Calculate and Reduce Them
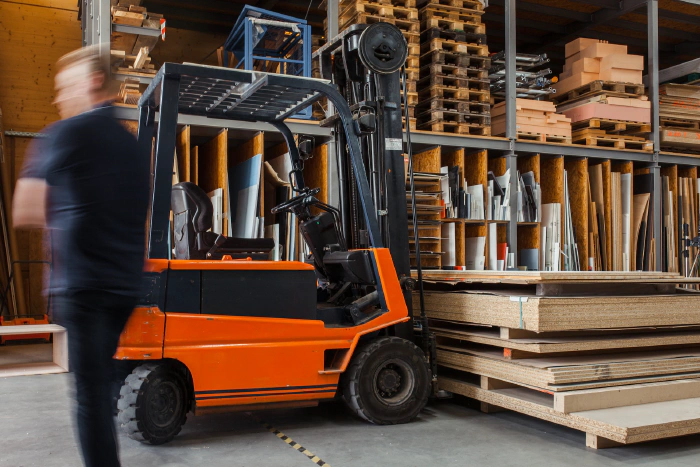
Holding onto inventory can be more expensive than you might think. Inventory carrying costs, also known as inventory holding costs add up. The longer you hold onto stock, the higher those costs become.
That’s why optimizing your inventory to keep stock for only as long as is necessary to meet demand is so important. In this article, you’ll discover exactly what inventory carrying costs are, how to calculate them and most importantly, how to reduce them.
Table of Contents
- What are Inventory Carrying Costs?
- Types of Inventory Carrying Costs
- Why Is It Important to Calculate Inventory Carrying Costs?
- Factors That Can Affect Inventory Carrying Costs
- How to Calculate Inventory Carrying Costs
- 8 Tips for Reducing Inventory Carrying Costs
- Manage Inventory Carrying Costs With The Right Software
What are Inventory Carrying Costs?
Inventory carrying costs are expenses related to holding and storing unsold goods. They include salaries, transportation, taxes, insurance, depreciation, shrinkage and the costs of warehousing. One of the biggest inventory carrying costs is the opportunity cost of not selling an in demand product.
Types of Inventory Carrying Costs
Some inventory carrying costs are more obvious, like storage, insurance and handling but many costs go unnoticed. Let’s review them:
-
Storage costs. If you use a 3PL, you’ll be charged by the shelf, pallet or item for storing stock. The longer an item is with your 3PL, the more it will cost to store. If you have your own warehouse, there will still be storage costs involved, based on your rent and the amount of space an item uses.
-
Insurance costs. Your inventory is how you make money so you need to insure it. That isn’t free and the more products you store, the higher the cost is.
-
Handling costs. Every action attached to a product has a cost. From putting it on the right shelf in a warehouse to labeling, to using machinery to maneuver it, you need to account for every touchpoint.
-
Capital costs. This is often the largest cost to a business. It includes the product price and any other interest or associated fees.
-
Shrinkage. If you never sell a product because it’s lost, stolen, damaged or for any other reason, your inventory carrying costs are higher. Insurance can lessen the impact.
-
Product obsolescence. If a product is at the end of its lifecycle, it’s obsolete and you can’t sell it. It has a similar impact to shrinkage but insurance is less likely to cover this problem. Instead, you could opt for large discounts, donations or offloading everything to a liquidator, instead of having to pay for disposal.
-
Taxes. Most goods have taxes attached to them. The more you import to your warehouse, the higher your tax burden will be.
-
Administrative costs. Keeping track of the stock you have with inventory checks, software and other admin is necessary, but it isn’t free. It’s another cost you need to be aware of.
-
Employee costs. Making sure your inventory is delivered on time, counting stock, receiving goods and many other inventory related tasks need employees. You need to pay their salaries and any other associated social insurance contributions
-
Opportunity costs. Holding onto stock that isn’t in demand takes up space that could be used for in-demand inventory. This means you’re not earning revenue and that counts as a cost too.
Why Is It Important to Calculate Inventory Carrying Costs?
If you don’t know how much you’re spending on inventory carrying costs, you don’t know how much profit your business is making, or worse still, how much it’s losing. Once you know your basic inventory carrying costs, you can assess the extra financial burden overstocks will cause.
You also need to factor in the cash flow that’s tied up when you hold too much inventory. Even if you’re bringing in a lot of revenue, not having enough cash can stop potential marketing opportunities, investments or sales. Knowing what your inventory carrying costs amount to makes inventory planning easier and more realistic.
Factors That Can Affect Inventory Carrying Costs
A lot of factors can affect inventory carrying costs and it’s important to be aware of them so you can prepare and manage your inventory accordingly.
Seasonality and Demand Fluctuations
Inventory forecasting requires an understanding of seasonality. How does demand change in the winter for a trench coat in comparison to the summer months? When you’re doing retail demand planning, you need to account for all demand fluctuation possibilities. If demand for certain products unexpectedly reduces and you’re holding a lot of stock, your inventory carrying costs will increase.
💡Pro Tip: Avoid unexpected changes in demand and automatically account for seasonality in your inventory forecasts with Singuli’s Advanced Forecasting tools.
Supplier Lead Times
The longer a supplier’s lead time is, the longer you have to hold onto inventory, as you’ll need to buy more to account for the extra time. It’s important to build and maintain strong supplier relationships with as many vendors as possible. That way, you can always order and have stock delivered in the shortest time possible, meaning you’re not paying for unnecessary storage costs.
💡Pro Tip: Maintain optimum stock levels and adjust to sudden changes by using Singuli to manage multiple vendors and products with different lead times.
Quality of Inventory Planning and Management
If your inventory planning and management is sub standard, your inventory carrying costs will rise. Your chances of overstocks will increase, your supplier relationships will deteriorate and if you don’t have a good order fulfillment system in place, you could hold onto stock for too long.
📌Get Started: Optimize your inventory levels and reduce overstocks. Use Singuli to replenish the right amount of stock at the right time so your inventory costs stay low.
Inventory Turnover Rate
A slow inventory turnover rate (ITR) means you’re holding onto stock for longer. Some products inevitably have a longer ITR than others but it’s important to forecast accurately so you know which products are staying on your selves for longer and increasing your carrying costs.
💡Pro Tip: Take advantage of Singuli’s detailed Reporting & Analytics to create a forecast that meets the strategic needs of your business.
How to Calculate Inventory Carrying Costs
To work out your inventory carrying cost, you need to know your inventory holding amount. This is the sum of your stock service cost, capital cost, storage space fee and inventory risk charge. By using this formula, you can accurately assess your holding costs as a percentage.
$$\text{Inventory holding cost} = \frac{\text{inventory holding amount}}{\text{inventory value}} \times 100$$
Inventory holding cost example:
- Inventory holding amount = $400,000
- Inventory value = $1,200,000
Inventory holding cost = $400,000 ÷ $1,200,000 × 100 = 33.33%
8 Tips for Reducing Inventory Carrying Costs
Now that you know what inventory carrying costs are and how to calculate them, it’s important to try and reduce them wherever possible. Here are eight tips for reducing inventory carrying costs:
1. Keep Less Inventory On Hand
Many businesses understandably worry that they’ll experience stockouts. That would cause a loss of sales, potentially a loss of customers and other related costs. With that in mind, they hold more stock but this has a cost too, as we’ve already seen.
The best solution is to keep less inventory on hand but to calculate safety stock. This allows you to hold onto the minimum amount of stock necessary to meet demand without causing overstocks. It’s especially important for your most valuable inventory, which you can determine with ABC analysis.
💡Pro Tip: Give context to your sales history with Singuli’s ABC reporting and make it part of your wider inventory planning.
2. Reconfigure Your Warehouse Space
Are you using the most efficient containers for your items? Could you fit more into the same space without compromising access? Is there an opportunity for shelving so you can store up, instead of just across? Reconfiguring your warehouse space can help you save a lot on carrying costs so it’s worth considering.
💡Pro Tip: Get a holistic view of your inventory data with Singuli’s Reporting & Analytics. Track not only inventory data, but also marketing, promotions, site traffic, historical sales and customer behavior. You’ll have all of your information in one place, ready to use in inventory forecasting and planning.
3. Increase Inventory Turnover
Your inventory turnover (ITR) is the quantity of stock you sell over a particular period. The higher that number is, the less likely you are to cause overstocks. The number needs to be balanced and you need accurate demand forecasting in place to make sure you don’t cause stockouts instead.
📌Get Started: Avoid stockouts and overstocks by understanding the perfect inventory turnover rate (ITR) with Singuli’s Advanced Demand Forecasting.
4. Reorder and Replenish at The Right Times
Reordering and replenishing too early or too late is a quick way to increase costs. When you understand the perfect reorder point for each product, you can order just the right amount at just the right time.
💡Pro Tip: Use Singuli’s location-level forecasts and replenishment alerts to optimize your inventory. If you have a mixture of retail and e-commerce channels, Singuli bases your forecasts on distinct models to reflect the variations in inventory patterns.
5. Account for Product Size Curves
Product forecasting becomes more difficult when you have multiple sizes and attributes. If you forecast the right total amount for a selection of pants but you have too many in size L and not enough in size XL, you create an overstock and a stockout problem. To avoid that, you need to account for product size curves.
💡Pro Tip: Automatically compute the right size curve for every sized-based product in your assortment with Singuli’s size-based forecasting and planning tools.
6. Negotiate Supplier Pricing and Lead Times
There’s a balance to strike with suppliers between making sure you’re keeping them on side and making sure you’re not taking the burden of risk. For example, who is responsible for damage caused to products in delivery and who pays for administration costs when goods are in their possession.
Make sure your contracts reduce your risk and put contingencies in place for slow lead times or delivery delays. Keep track of any costs and keep everyone informed for a stronger and fairer supplier relationship.
💡Pro Tip: Use Singuli to automate your inventory planning. Automatically sync your expected receipts with the warehouse, keep track of your landed costs and share ETA dates with your freight forwarder with Purchase Orders & Shipments.
7. Allocate The Right Amount of Inventory to Each Sales Channel
In a similar way to accounting for size curves, you also need to account for sales channels and locations. The right quantity of stock across the business doesn’t automatically equate to the right amount of inventory for each channel. Put processes in place to make sure each channel is stocked accurately.
💡Pro Tip: Use Singuli’s real-time, channel-aware forecasting to maximize sales in every location.
8. Make Data-Backed Decisions With Inventory Optimization Software
Inventory optimization software allows you to analyze all your data and to turn it into accurate forecasts. With the right software, you can account for size curves, forecast correctly for each sales channel, reorder at the right times, make sure you have adequate safety stock and more.
📌Get Started: With Singuli’s [Advanced Forecasts(/features/forecasts)], it’s easy to analyze historical data, market trends and customer inputs, which saves you or your inventory planner time and increases forecast accuracy.
Manage Inventory Carrying Costs With The Right Software
You know what inventory carrying costs are, how to calculate them and how to reduce them. This is all made easier with the right software. Singuli collates all your data from sales to lead times to product marketing and uses relevant information to create accurate inventory forecasts. This allows you to order just the right amount of stock to avoid stockouts and minimize carrying costs.
Inventory Carrying Costs FAQ
What Are Inventory Carrying Costs Examples?
The costs of holding stock are called carrying costs or holding costs. They include taxes, insurance, storage costs, employee costs and opportunity costs.
How Do You Manage Inventory Carrying Costs?
There are a number of ways to manage inventory carrying costs, including holding less inventory, reconfiguring your warehouse space and managing your inventory turnover rate. This is all easier with the right inventory optimization software.
What Are The 3 Typical Inventory Carrying Costs?
The three typical or most obvious carrying costs are:
- Storage costs
- Handling costs
- Insurance costs
Forecast demand, issue and track POs, reorder on autopilot, and step up your reporting game across multiple channels and locations. Get in touch to see how Singuli can help you optimize your inventory.