Weeks of Supply Formula: Is it Right For Your Business?
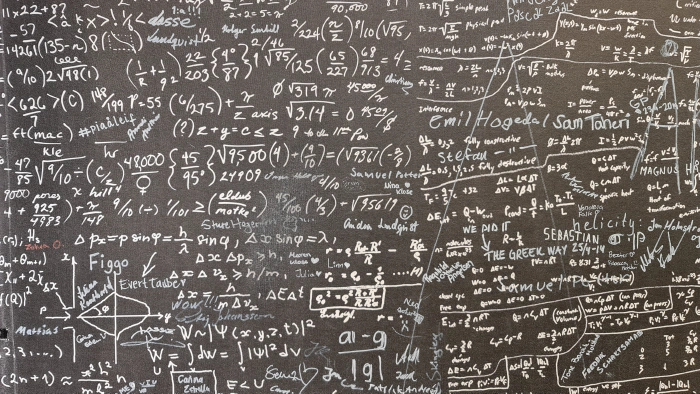
As a retailer or somebody who runs an e-commerce store, you know how important it is to manage and plan your inventory. Many businesses use the weeks of supply formula (WOS) to make sure they have enough inventory to meet demand.
Once you understand weeks of supply, it can benefit your business but it’s far from perfect. Let’s discover what weeks of supply is, how to calculate it, what its benefits are, where pitfalls exist, what the alternatives are and the best ways to optimize your inventory planning.
Table of Contents
- What is Weeks of Supply (WOS)?
- Why are Accurate Weeks of Supply Calculations Important?
- How to Calculate Weeks of Supply
- How Granular Should Weeks of Supply Be?
- Pitfalls of Weeks of Supply
- Setting Weeks of Supply Targets
- Weeks of Supply Alternatives
- Optimize Your Inventory Planning
- Weeks of Supply FAQs
- Is Weeks of Supply Right For Your Business?
What is Weeks of Supply (WOS)?
Weeks of supply (WOS) is a frequently used metric in inventory planning that compares the inventory you have against anticipated demand. It’s a critical comparison to make and many retailers use WOS levels to assess inventory health and control their replenishment process. Accurate weeks of supply calculations help to make sure you have enough safety stock to meet demand until your next delivery without having to overstock.
Why are Accurate Weeks of Supply Calculations Important?
Even accurate weeks of supply calculations have pitfalls, as we’ll see later, but If you choose to use weeks of supply for inventory planning, you need to make sure your calculations are accurate. This way, you can optimize inventory levels, minimize stockouts and reduce spoilage.
Optimize Evergreen and Seasonal Inventory Levels
Evergreen products sell consistently all year, whereas seasonal products like Christmas decorations or sunscreen reflect a particular time of year or event. Good inventory planning considers seasonal forecasts so you know how much to reorder without filling up the warehouse with excess inventory.
💡Pro Tip: Get a holistic view of your inventory data with Singuli’s Reporting & Analytics. Track not only inventory data, but also marketing, promotions, site traffic, historical sales and customer behavior. You’ll have all of your information in one place, ready to use in inventory forecasting and planning.
Avoid Stockouts and Reduce Backorders
According to a PWC Global Consumer Insights Pulse Survey, 37% of respondents say they would shop at multiple retailers online and in brick-and-mortar stores to meet their needs. A major is that the product they’re looking for is out of stock. A forward weeks of supply calculation (more on this below) helps to avoid stockouts and reduces the number of backorders needed to meet demand.
Minimize Overstocks
If you don’t want to incur carrying costs or take up valuable space, you don’t want overstocks. They’re bad for cashflow and leave stock open to spoilage. Accurate WOS helps to reduce the possibility of overstocks happening.
Create Better Supplier Relationships
Understanding your inventory levels in advance means you can keep orders consistent and communicate with your suppliers earlier. Accurate weeks of supply makes this easier and helps create better supplier relationships.
Forecast demand, issue and track POs, re-order on autopilot, and step up your reporting game across multiple channels and locations. Get in touch to see how Singuli can help you optimize your inventory.
How to Calculate Weeks of Supply
There are two main formulas for WOS, backward weeks of supply formula and forward weeks of supply formula. Let’s use an example to see how they work:
Let’s say you have a women’s clothing boutique and want to calculate weeks of supply for three products: orange shorts, a beige coat and a high heeled shoe. The eight week sales (8WS) and the current on-hand (OH) are shown below for these products.
Product | 8WS | OH |
---|---|---|
🩳 | 200 | 1200 |
🧥 | 300 | 1500 |
👡 | 400 | 2400 |
Backward Weeks of Supply Formula
The simplest weeks of supply calculation is a “backward looking” WOS, which takes the current on-hand (OH) inventory and divides it by the average unit sales per week, known as weekly velocity (WV):
$$\text{WOS}_b = \frac{\text{OH}}{\text{WV}_b}$$
In this case, since we have eight week unit sales, we first calculate the WV and then work out WOS as follows:
Product | 8WS | OH | WVb | WOSb |
---|---|---|---|---|
🩳 | 200 | 1200 | 25 | 48 |
🧥 | 300 | 1500 | 37.5 | 40 |
👡 | 400 | 2400 | 50 | 48 |
You or your planner might be satisfied because you have respectively 48, 40 and 48 weeks of supply for the three products. This means that if the past eight weeks are representative of the next 40+ weeks, you should have enough inventory to meet the demand. But it’s a big if.
You’d be right to ask a few important questions here:
What happens if the demand changes seasonally?
Suppose that the weeks of supply calculation was carried out on March 1st and the demand for shorts picks up in the summer months as follows:
Product | Metric | March | April | May | June | July | August | September |
---|---|---|---|---|---|---|---|---|
🩳 | Demand Forecast | 200 | 1000 | 1500 | 4000 | 2000 | 1000 | 200 |
🩳 | OHeop | 1000 | 0 | 0 | 0 | 0 | 0 | 0 |
You can see that by the end of April the original 1,200 units of shorts are out of stock, even though the backward WOS calculation said we had 48 weeks of supply! This is one reason why the backward weeks of supply numbers need to be interpreted carefully: the calculation does not account for seasonal fluctuations in demand. Even averaging the velocity over a longer period may not suffice if the variance of the demand is high.
📚 Further reading: Demand Forecasting: Your Guide to the Future
Why aren’t we considering planned receipts?
By looking at historical data alone, we ignore the possibility of planned receipts. What happens if our shorts planner has ordered inventory to cover the increase in demand?
Product | Metric | March | April | May | June | July | August | September |
---|---|---|---|---|---|---|---|---|
🩳 | Sales | 200 | 1000 | 1500 | 4000 | 2000 | 1000 | 200 |
🩳 | Receipts | 0 | 2000 | 0 | 2500 | 0 | 0 | 0 |
🩳 | OHeop | 1000 | 2000 | 500 | 1500 | 0 | 0 | 0 |
Now we’re not in trouble in April because 2000 units are set to arrive, but we do quickly stock out after that. In particular, if we computed WOS on April 1st, we’d see a velocity of 37.5 and ownership of 3000 units, giving 80 weeks of supply, but by June we’re out of stock again.
Forward Weeks of Supply Formula
To calculate a forward WOS, you need to include a demand plan in your formula, which allows you to consider a forecasted velocity instead of a velocity derived purely from historical sales.
You’ll also take receipts into consideration. Let’s work with the shorts example:
Product | Metric | March | April | May | June | July | August | September |
---|---|---|---|---|---|---|---|---|
🩳 | Demand Forecast | 200 | 1000 | 1500 | 4000 | 2000 | 1000 | 200 |
🩳 | Velocity Forecast | 150 | 312.5 | 687.5 | 750 | 385 | 150 | n/a |
As you can see, the forecasted velocity at the start of the month is based on the demand forecast for the next eight weeks (assuming months are four weeks for simplicity).
Forecasted On-Hand
You’ve worked out your forecasted velocity so now you need to forecast the inventory you’ll have on hand. Let’s look at the table below, sometimes called a ladder plan:
Product | Metric | March | April | May | June | July | August | September |
---|---|---|---|---|---|---|---|---|
🩳 | OHeop-1 | 1200 | 1000 | 2000 | 500 | 0 | 0 | 0 |
🩳 | Receipts | 0 | 2000 | 0 | 2500 | 0 | 0 | 0 |
🩳 | OHbop | 1200 | 3000 | 2000 | 3000 | 0 | 0 | 0 |
🩳 | Demand Forecast | 200 | 1000 | 1500 | 4000 | 2000 | 1000 | 200 |
🩳 | Sales Forecast | 200 | 1000 | 1500 | 3000 | 0 | 0 | 200 |
🩳 | OHeop | 1000 | 2000 | 500 | 0 | 0 | 0 | 0 |
Now we have the forecasted OH for the beginning and end of the period (BOP and EOP respectively), which gives us enough information for the forward weeks of supply formula.
$$\text{WOS}_f = \frac{\text{current oh}{\text{velocity}_f}_f}$$
Finally, you can combine the velocity and the ownership to produce a forward WOS at the start of each month:
Product | Metric | March | April | May | June | July | August | September |
---|---|---|---|---|---|---|---|---|
🩳 | OHbop | 1200 | 3000 | 2000 | 3000 | 0 | 0 | 0 |
🩳 | Velocityf | 150 | 312.5 | 687.5 | 750 | 385 | 150 | n/a |
🩳 | WOSf | 8 | 9.6 | 2.9 | 4 | 0 | 0 | n/a |
Seeing this far enough in advance (i.e. with enough time to place an order with a supplier), you or your planner could decide that forward WOS starting in May was too low and that more receipts were required.
How Granular Should Weeks of Supply Be?
A forward WOS resolves some of the challenges posed by a backward WOS but there are still questions that need answers. One of the most important involves aggregated data. For accurate stock levels, you need to make your weeks of supply as granular as possible but using WOS for aggregated data has its own challenges.
WOS is often aggregated to deal with sized products. Suppose our 🩳 come in five sizes and to-date, the planner has been doing their analysis at the style-color level. One possible stock keeping unit (SKU) parameter is size. When we asses this, the story changes:
Size | Velocityf | OHbop | WOSf |
---|---|---|---|
XS | 5 | 1000 | 200 |
S | 45 | 50 | 1.1 |
M | 70 | 50 | 0.8 |
L | 20 | 50 | 2.5 |
XL | 10 | 50 | 5 |
– | – | – | – |
All | 150 | 1200 | 8 |
As we worked out WOS using an average OH and WV, the nuance of the size curve has been lost and it looks like we’re in a good position when we’re not. To fix this, you could work out the weeks of supply for each size and then combine them. But how?
One way would be to track the minimum and maximum forward WOS across the sizes. Another would be to take a median:
Product | WOSf | WOSf,min | WOSf,max | WOSf,med |
---|---|---|---|---|
🩳 | 8 | 0.1 | 200 | 2.5 |
🧥 | 5 | 5 | 5 | 5 |
👡 | 20 | 0 | 25 | 0.2 |
As you can see, it can be very tricky to interpret the average forward weeks of supply. In the case of the 🩳, we have somewhere between 0.1 (min) and 200 (max) WOS and 50% of the sizes have less than 2.5 weeks (median). At the same time the weighted average WOS is eight, which reflects something completely different.
Over time, you’ll gather more data, which will help you identify trends and outliers but no matter how granular you are with weeks of supply, there’s no guarantee of accuracy.
Pitfalls of Weeks of Supply
Whether you use backward, forward or even aggregated WOS, you’re going to face challenges. Some will already be apparent but let’s take a closer look:
Backwards Focused
Unless every season has exactly the same level of demand, backward weeks of supply won’t work. You’ll soon have stockouts or overstocks.
Aggregating Data
WOS can be done at a SKU level but as you’ve seen in the example, it makes it extremely difficult to manage. Standard weeks of supply doesn’t aggregate data and aggregating minimum, maximum or median WOS leaves a lot of margin for error.
Insufficient Data
With weeks of supply, you’re using limited data to calculate your optimum stock levels. You know your forecasted velocity, your forecasted OH and even some SKU level data but you’re not considering marketing campaigns, DTC (direct-to-consumer) events or any other influential data points.
Quality of Data Inputs
If the data going into your weeks of supply calculations is bad, the data coming out will be even worse. This isn’t a direct pitfall of WOS alone but using software with better automations and reducing the possibility of human error will help with inventory planning.
📌Get Started: With Singuli’s Purchase Orders & Shipments, you can track exactly who did what and when they did it. Every change is linked to a user and logged automatically.
Ignores Spikes in Demand
Things happen that change the popularity of a product all the time. Picture your favorite superstar celebrity. Now, picture them on a beach, two weeks before the holidays start, about to take a selfie featuring your product. This was completely unplanned but as soon as the world sees it, you see a huge spike in demand. Weeks of supply can’t plan for that.
Setting Weeks of Supply Targets
Now that you understand the pitfalls of WOS, you can consider them when setting your weeks of supply target for each item.
Fluctuations in Demand
For products with less historical data, the fluctuations in demand will be higher as your forecasting information is weaker. Over time, this will improve but other factors in demand variability, such as changes in weather are harder to foresee.
📚**Further reading:** 14 Steps to Launch a New Product
Supplier Changes
You may have reason to change your suppliers over time and even if you stick with the same suppliers, their lead times and working practices may change. Unfortunately, not all suppliers are reliable when it comes to delivery dates and fill rates, and even the most reliable can be caught out by something like a global pandemic, so you need to expect the unexpected.
Stockout Costs
Exactly how much stockouts costs can be hard to calculate. Of course, you’ll miss out on selling the particular products that are no longer available but there’s more to consider. For example, if you have stockouts a lot, customers may never come back and if you had a bundle connected to the products that had a stockout, you could miss out on selling items that are still in stock too.
Carry Costs
There is a cost to holding onto stock. You need to pay for storage and the value of products often depreciates over time. Plus, you’re taking up space that could be used for better selling items.
Keeping all of this in mind, you can think about how to set a weeks of supply target or find a WOS alternative. If you stick with weeks of supply, remember that higher fluctuations in demand, supplier changes and stockout costs increase the optimum weeks of supply target whereas higher carry costs decrease the optimum WOS target.
Weeks of Supply Alternatives
The goal of weeks of supply is to make sure you have enough inventory to meet demand. It’s a good tool but as you’ve learned in this article, there are several pitfalls. You can use the weeks of supply formula in combination with other inventory planning tools or you can find better suited alternatives.
For example, some companies use Turn, which measures the number of times the average inventory is sold and replaced over a set time period, alongside WOS.
Or you could avoid the weeks of supply metric altogether and opt for the fill rate metric or service level view. These options provide a far higher level of accuracy and answer the important question:
What proportion of my forecasted demand can I fill with the expected inventory?
📌Get Started: Use Singuli to make sure your inventory levels are just right. With reorders on autopilot, you’ll always purchase the right quantities to the SKU level and you’ll never miss out on a potential sale.
Optimize Your Inventory Planning
However you choose to manage your inventory, there are a few important factors to always keep in mind:
Keep on Top of Minimum Order Quantities (MOQ)
Many suppliers set MOQs to protect their business viability. When you’re working out the inventory you need to bring in to meet demand, you may consider supplier MOQs. If you always need more than the MOQ in place, MOQs aren’t a problem but if you need less than the MOQ, you have to be careful not to overstock.
There are a few things you can do to stockouts or overstocking. Start by making sure your forecasts are as accurate as possible for the months ahead, so you can plan accurately.
📌Get Started: With Singuli’s Advanced Forecasts, it’s easy to analyze historical data, market trends and customer inputs, which saves you or your inventory planner time and increases forecast accuracy.
If you can forecast demand, you’ll have a better starting point to negotiate with your supplier. You can make orders that meet their MOQs, but ask them to hold onto the stock you don’t need immediately and ask to pay on arrival. This helps with cash flow and reduces your holding costs. If the supplier is completely unwilling to work in this way, you might want to look for an alternative. Strong supplier relationships are key to good inventory planning.
Analyze Performance and Stock
There’s a moment that most businesses dread: thinking you have stock on hand for a customer and then finding out you don’t, even though your system says you do. Whether you’ve lost inventory through theft, damage or something else entirely, you need to be aware.
The best way to keep on top of your inventory levels is to conduct regular audits. You can do full stock checks periodically but this often means that big gaps are left between each one. An alternative option is to perform regular cycle counts, which involves counting a small portion of stock daily or weekly. Over time, you’ll have checked your whole inventory, without having to shut down operations.
Forecast Seasonal Fluctuations
One of the pitfalls of backward weeks of supply is the inaccuracy of forecasting seasonal fluctuations. If you don’t know when there will be spikes or drops in demand, you can’t accurately order inventory.
Marketing, promotions, changes in weather, political events and even global pandemics can affect demand so make sure you have a planning system that’s ready for every eventuality.
💡Pro Tip: Get a holistic view of your inventory data with Singuli’s Reporting & Analytics. Track not only inventory data, but also marketing, promotions, site traffic, historical sales and customer behavior. You’ll have all of your information in one place, ready to use in inventory forecasting and planning.
Keep Strong Supplier Relationships
Suppliers have a lot to manage. They have to deal with unexpected fluctuations, seasonality and supply chain issues, which can all cause challenges for you. Often, the biggest effect is on lead times. The difference between expected lead times and actual lead times varies, which can cause you to have stockouts or overstocks.
It’s important to keep up good supplier relationships so you’re aware of any challenges they’re having. This will help you prepare, especially if you’re tracking variability properly and basing forecasts on tailored models.
💡Pro Tip: Use Singuli’s location-level forecasts and replenishment alerts to optimize your inventory. If you have a mixture of retail and e-commerce channels, Singuli bases your forecasts on distinct models to reflect the variations in inventory patterns.
Weeks of Supply FAQs
Let’s answer some of the most commonly posed questions on weeks of supply:
When Should I Use the Weeks of Supply Formula?
If your business is stable and you’re comfortable operating at the SKU level then Weeks of Supply is not a terrible metric. But we recommend using Singuli for greater accuracy and less stress. If you decide WOS is right for you, you need to keep on top of it and use it across all stages of your inventory planning cycle.
What’s the Difference Between Backward and Forward Weeks of Supply?
Backward WOS forecasts the number of weeks you have inventory available for based on historical data only. Forward WOS combines information about historical data, forecasted demand and receipts for a more accurate calculation.
What Are The Alternatives to Weeks of Supply?
There are many alternatives to WOS but at Singuli, we recommend using fill rate and service levels when trying to ascertain if you have adequate inventory. To see if you have too much inventory you can forecast your deviation from the optimal inventory levels.
Is Weeks of Supply Right For Your Business?
You’re fully aware of what weeks of supply is, you know how to calculate it, how important accuracy is, the level of granularity needed and how to set targets. You also know the pitfalls of using WOS, some alternatives and some of the most important tips on optimizing your inventory. Now, it’s time to decide whether to use WOS or something like Singuli for your inventory planning.
Forecast demand, issue and track POs, reorder on autopilot, and step up your reporting game across multiple channels and locations. Get in touch to see how Singuli can help you optimize your inventory.